Color Fastness to Crocking/Rubbing Test, ISO 105 X12 (With Video)
- Benson Li
- Sep 26, 2016
- 5 min read
Updated: Mar 28, 2024
What is color fastness?
Color fastness is a term used in the textile industry to describe the resistance of a fabric against color fading or color transfer.
There are different types of colour fastness. The common ones are:
Color fastness to Washing
Color fastness to Light
Color fastness to Crocking/Rubbing
Color fastness to Perspiration
For bag manufacturing industry, we are usually most concerned with color fastness to Crocking/Rubbing, and this is what we will be focusing on in this article.
What does Crocking mean and why is it important?
Crocking means the transfer of color from one fabric onto another by rubbing. A fabric with poor color fastness would transfer its color easily onto other fabrics, especially to white color fabrics.
No one wants his/her white shirt to get stained by his/her backpack. That is why color fastness to Crocking/Rubbing is especially important in the bag manufacturing industry.
How to determine the color fastness of a fabric?
We can check the color fastness of a fabric by running a test. The test methods that we usually use for Crocking/Rubbing are called "BS EN ISO 105 X12" and "AATCC 8". We need a Crockmeter to carry out this test and below is how it typically looks like.
During the test, a white conditioned rubbing cloth would be rubbing on the test specimen, back and forth in a straight line for 10 cycles with downward force. Usually, two tests would be made, one with a dry rubbing cloth and another with a wet one.
Then, after the test is done, the tested rubbing cloth should be evaluated against the grey scale under decent light source.

The color fastness to Crocking/Rubbing is categorised from 1 to 5. The higher the number, the better the fastness.
Ideally, we want no colour transfer at all. Unfortunately, it is not possible in real life. So, what should be considered acceptable? Below is the standard most companies use:
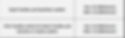
For Dyed Textiles such as Polyester and Nylon, and Synthetic Leather such as PVC and PU, the common standard is Dry: 4.0 and Wet: 3.0.
For Print Textiles, Denim, Canvas, Velvet Textiles and Genuine or Suede Leather, the common standard is Dry: 3.0 and Wet: 2.0.
What are the Factors that affect color fastness?
Material composition affects a great deal for color fastness. By nature, some materials are always better than others when color fastness is concerned. For instance, the color fastness of Polyester and Nylon fabrics are normally one grade better than Denim's and Canvas's. Therefore, the common standard for Denim, Canvas, Print Textiles, Velvet Textiles and Genuine or Suede Leather is set at a relatively lower level, which is only Dry: 3.0 and Wet: 2.0, as people in the industry understand and expect that it is difficult for these materials to achieve a high color fastness standard. As such, during product development, when these fabrics are involved, it is better to pay special attention to make sure that the material suppliers would handle the fabrics carefully. Otherwise, you might end up with a product that will stain clothes.
Color also affects color fastness. Materials in darker colors tends to have lower color fastness than lighter color materials. Also, due to the chemical properties of the dye, there are a few colors that are now widely known to be more problematic, such as Red, Navy Blue & Black.
Other factors that affect color fastness include the specific dye used in the dyeing process, the dyeing process itself, any additives, fixatives or softeners used, and the way of washing of the fabrics etc.
Extended Reading: Impact of Dyeing Techniques on Color Fastness
While our main focus here is on understanding Color Fastness to Crocking/Rubbing Test and how it's a crucial test in maintaining quality control within the textile industry, it's beneficial to delve deeper into related areas that influence the outcome of this test. One such area is the type of dyeing technique employed in the textile's production process.
The method used to dye a fabric significantly impacts its color fastness, making this topic a valuable extension of our conversation on ISO 105 X12. Whether you're a textile manufacturer, designer, or enthusiast, understanding the dyeing process opens up broader insights into achieving optimal color fastness. Here’s a closer look at the impact that various dyeing techniques have on the durability and longevity of fabrics in terms of their color fastness:
Fiber Dyeing
Before the yarn is spun, fibers can be dyed to create a color core within the material, known as fiber or stock dyeing. This method is common in producing heathered or mélange effects on fabrics typically seen in sweaters and suiting materials. Because the dye penetrates deep into the fiber, this technique generally enhances the color fastness against crocking, making it a preferred choice for manufacturers looking for long-lasting color.
Yarn Dyeing
Yarn dyeing happens post-spinning but prior to the weaving or knitting of the textiles. Common methods include skein dyeing, where yarns are dyed in skein form, and package dyeing, where yarns are wound on a small package and then dyed. Compared to fabric dyeing, yarn dyeing ensures better color penetration and consequently better fastness. Textiles with multiple colors or patterns, like plaids, stripes, and checks, often employ yarn dyeing to achieve their intricate designs.
Piece Dyeing
The most common form of dyeing is piece dyeing, in which the fabric is dyed after being woven or knitted. This method allows a quick response to fashion trends as manufacturers can dye the fabric according to demand. However, this method can sometimes result in less color fastness compared to when the individual fibers or yarns are dyed, as the color may not penetrate as fully to the core of each fiber throughout the fabric. Technologies like jet dyeing machines and high-temperature processes have been developed to enhance the color fastness of piece-dyed fabrics.
Garment Dyeing
In garment dyeing, the product is constructed in white or greige and then dyed as a finished product. This method is excellent for achieving a unique look and vibrant colors. However, it could pose a challenge for color fastness to crocking, as the constructed garments might not receive an even dye penetration throughout all the layers and stitching, which can result in variable fastness results.
Dye Selection Consideration
The type of dye used in these processes also significantly influences the final fastness properties. Reactive and vat dyes are known for their superior fastness qualities and are favored for materials that demand high durability. Acid dyes, while vibrant, may not have the same level of fastness and are typically used for less durable items or specialty fabrics where high fastness is not the primary concern.
Innovations in Dyeing for Enhanced Fastness
It's worth noting that advancements in dye formulations and dyeing techniques continue to emerge. These include the use of microencapsulation technologies, nano dyeing, and digital printing that offers better control over dye placement and fixation on the fabric, consequently improving fastness to crocking.
In conclusion, each dyeing technique has its own set of benefits and potential issues concerning color fastness to crocking. By choosing the right method and closely controlling the dyeing process, fabric manufacturers can enhance the color longevity and thus the consumer appeal of their products. It is this meticulous attention to detail in the dyeing stage that defines the quality and marketability of the final textile product.